- Automotive
- Aviation
- Building & Construction
- Corporate
- Corrections & Prison Systems
- Evaporative Cooling
- Farm & Agriculture
- Home & Residential
- Hospitality & Dining
- Military & Government
- News
- Outdoor Work Applications
- Pets & Animals
- Safety
- Small Business & Trades
- Sports & Outdoors
- Warehouse & Industrial
Hot working conditions cause productivity and profits to plummet
You rely on your employees to perform their job accurately, effectively, and efficiently in order to maintain an optimal profit margin. When their performance and productivity drops, it can have a significant impact on your bottom line, your perception among your customers, and your overall success. During the summer months, hot temperatures often create suboptimal working conditions which negatively impact worker productivity and result in higher employee turnover rates.
For this reason, it’s critical to maintain a comfortable work environment for your employees. At Portacool, we understand that hard data often paints the most compelling picture and allows you to understand the true impact hot working conditions have on your business. Below are some of the ways in which excessive heat can cause your productivity and profitability to drop.
Impact of Excessive Heat on Worker Productivity
When temperatures in your work environment become very hot, your employees’ ability to regulate their body temperature becomes increasingly compromised. This results in a variety of issues which may impact their performance and productivity, including:
- Fatigue
- Reduced cognitive function
- Reduced motor skills
- Dizziness
- Nausea
These issues often result in increased errors, a reduced capacity to complete work in a timely manner, and in severe instances, it can result in serious accidents and injuries.
There have been numerous studies conducted which demonstrate the ways in which heat stress negatively impacts worker productivity. The reduction in your employees’ capacity drops swiftly as the ambient temperature rises:
- 95% at 77°F with a relative humidity of 30%
- 68% at 95°F with a relative humidity of 50%
- 25% at 104°F with a relative humidity of 80%
This study used the ambient temperature in the shade to measure the loss in productivity. A different study used the Wet Bulb Globe Temperature (WBGT) to evaluate the loss in worker productivity. The WBGT encompasses a broader range of factors, including temperature, humidity, radiant heat and wind speed. The results of this study found that productivity losses are 80% higher for employees working in the sun compared to those working in the shade. For businesses with employees working outdoors, the negative impact of heat stress can be truly crippling to your productivity.
Are you curious about how these issues are impacting your business? You can use our Productivity Loss Calculator to better understand the dollars and productivity hours you’re losing due to hot temperatures at your work environment.
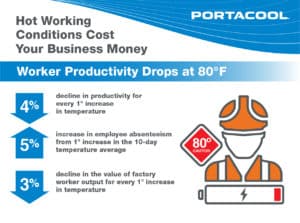
Worker Productivity Drops Significantly at Only 80°F
Several studies have identified 80°F as the temperature where worker productivity begins to seriously decline. A University of Chicago study found that production in manufacturing facilities drops by 4% on average for every degree the room temperature rises above 80°F. Similarly, a NASA study evaluating the impact of ambient temperature on worker errors found that mistakes rose dramatically above 80°F.
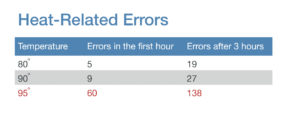
Employee Absenteeism Rises in Hot Working Conditions
Hot temperatures not only impact the performance of your workers, but they also reduce the number of employees you have on hand to get work done. The University of Chicago study referenced above also found that a 1°F increase in the ten-day temperature average resulted in a 5% increase in employee absenteeism. This increased absenteeism, combined with lower productivity of those employees in attendance, will have a significant impact on your output. Overall output drops 3% with just a 1 degree rise in the average daily temperature. In years where we experience severe summer heat waves that raise the average daily temperature by several degrees, it can result in a devastating drop to your worker output.
However, these figures only paint part of the picture when it comes to employee absenteeism. Heat-related illness from hot working environments forces workers to miss a significant number of days each year. In mild cases of heat illness, employees may be able to recover after only missing a few days of work. But when heat-related illness is severe, such as in cases of heatstroke, employees can potentially miss weeks or even months of work while they recover. Many workers also find that they’re unable to handle a full workload once they do recover.
These days missed from work and the ongoing loss of productivity when employees return can have a devastating impact on your business, severely reducing your output over the course of the year. In situations where workers develop permanent disabilities from a severe heat-related illness and are unable to return, you also incur financial costs associated with hiring and training new employees.
These costs are all avoidable by simply taking the steps to provide a cool, safe working environment.
Financial Costs of Heat-Related Productivity Losses
These productivity losses equate to staggering financial costs for businesses nationwide. Currently, the annual cost of lost work time and worker capacity due to heat-related issues in the United States is $100 billion, and this figure is expected to rise to $500 billion by 2050.
Certain industries are impacted more heavily than others, with food service, construction and agriculture being hit the hardest. In addition, certain regions of the country are impacted harder than others. In particular, the Southeast and Midwest have faced the highest economic losses from heat-related productivity issues. With its hot climate and high numbers of outdoor workers, Texas ranks as the state impacted the most by these economic losses. Currently, Texas businesses are losing approximately $30 billion per year, and this figure is expected to rise to $110 billion in 2050.
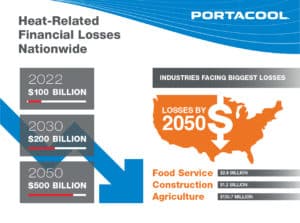
Maintaining a Cool Work Environment Is Critical to the Success of Your Business
Hot working conditions can have a devastating impact on your workers’ performance and productivity. This can significantly reduce your output and negatively impact the quality of the products you sell to your customers. When the loss of profits and damage to your reputation are combined with increased medical costs associated with work-related injury claims and potential legal costs in situations involving negligence, it can threaten the long-term financial viability of your business. Therefore, it’s critical that you take the steps necessary to provide a cool, safe working environment for your employees.
OSHA recommends that temperatures in work environments should fall within the range of 68-76°F to provide safe conditions for employees. If your business is located in an area where hot summer temperatures make it impossible to maintain these optimal ambient temperatures, it’s important to consider cooling solutions that will allow you to provide safe working conditions that will reduce employee injuries and help your team maximize their productivity.
Evaporative Coolers Are Ideal for Keeping Work Environments Cool
In many instances, air conditioning can be either cost prohibitive or impractical for maintaining cool temperatures at your work environment. Fortunately, you have another alternative that provides an effective, affordable, and environmentally sustainable cooling solution – evaporative coolers.
Evaporative coolers draw hot air over water-saturated cooling pads called evaporative media. This triggers an evaporation process that causes the air temperature to drop by as much as 30°F. This cooled air is then distributed throughout your work environment, providing your employees with the optimal ambient temperature to remain highly productive and avoid heat-related illness.
Keep in mind that in order for evaporative coolers to work effectively, they must have access to an outside air source. This makes them ideal for facilities which keep windows or loading docks open. They are also ideal for cooling outdoor work environments.
You’ll experience a variety of benefits when you use evaporative coolers instead of air conditioning to cool your work environment.
Lower Installation Costs
Air conditioning can be prohibitively expensive to install. In complex situations where ductwork must be installed, it can potentially cost over $100,000 to equip a large facility with air conditioning. You’ll eliminate these installation costs when you use evaporative coolers. Simply purchase the machines, plug them in and you’re ready to go.
Lower Energy Bills
Air conditioning requires a tremendous electrical output to power the system, resulting in huge monthly energy bills. Evaporative coolers only use as much electricity as is necessary to run the fan drawing air through the machine and the pump used to keep your evaporative media saturated with water. As a result, you can reduce your energy consumption by as much as seven times with evaporative coolers, creating a significant savings on your monthly energy bill.
Greater Environmental Sustainability
In addition to this reduced energy consumption, evaporative coolers don’t use any chemical refrigerants that may damage the environment (air conditioning relies on these chemicals to cool the air). For these reasons, evaporative coolers provide the most environmentally sustainable cooling solution.
Location Specific Cooling
For air conditioning to achieve your desired temperature, it must cool the entire space in your work environment. This can often be highly inefficient, especially in situations where your facility has very high ceilings or areas where employees aren’t working. Portable evaporative coolers can be moved around your facility to provide cooling in the exact areas where your workers are stationed for more efficient results.
Keep Your Work Environment Cool with a Portacool
Portacool has been the industry leader in evaporative cooling technology since 1990. We have a wide range of product lines to address just about any cooling application you may have, ensuring you can find the right Portacool for your specific work environment.
All Portacool evaporative coolers are made locally at our Center, Texas manufacturing facility. In addition, our evaporative media is made specifically for Portacool, ensuring it meets the exact specifications of your evaporative cooler for optimal performance.
Our commitment to quality products is matched by our commitment to customer service. You’ll benefit from our Portacool Protect™ program, which provides best-in-class:
- Warranties
- Technical Support
- Live Customer Service from Our USA-Based Customer Care Team
Visit a local retailer or contact us directly for large bulk orders.